Batteries are an essential part of our lives, powering devices across residential, commercial, and industrial sectors. As the demand for higher-performing, lightweight batteries continues to grow, so does the need for rigorous testing to ensure their safety and reliability.
Potential Hazards in Battery Testing
Despite years of research and development, batteries pose inherent risks, particularly when exposed to extreme conditions like physical impact, overheating, or overcharging. If a battery is dented or punctured there is a chance that harmful fluids can leak. If the battery is used outside its functional temperature range, or if it is overcharged, there is a chance of overheating. These risks are further classified into hazard levels by the European Council for Automotive R&D (EUCAR), and their widespread adoption has made them a standard reference for battery safety.
During one of the most concerning risks, thermal runaway, the battery generates more heat and energy than it dissipates, leading to a continuous increase in internal temperature until the chemical reaction subsides. To prevent such events and ensure safety, it is crucial to detect early indicators of thermal runaway and take immediate action.
Domestic and international groups such as the American National Standards Institute (ANSI), the Institute of Electrical and Electronics Engineers (IEEE), the International Electrotechnical Commission (IEC), the Society of Automotive Engineers (SAE), Underwriters Laboratories (UL), and the United Nations (UN) have compiled standards to outline how batteries should be tested. Batteries must undergo extensive examination to ensure chemistries are safe for consumer use. Environmental test chambers function to aid in this analysis, but special features must be put in place first.
Each EUCAR hazard level has been assigned a number 0 to 7, with 0 being no risk and 7 being the highest risk. Each subsequent level presents a new challenge in containing the hazards. Once the required hazard level is known, a set of safety features is added to the test chamber. Whether testing existing energy storage solutions or new chemistries and technologies for future innovations, consultation with a trusted manufacturer of environmental test chambers is the first step towards determining the necessary features to address your risk level and ensure personnel and product are kept safe during all stages of battery testing.
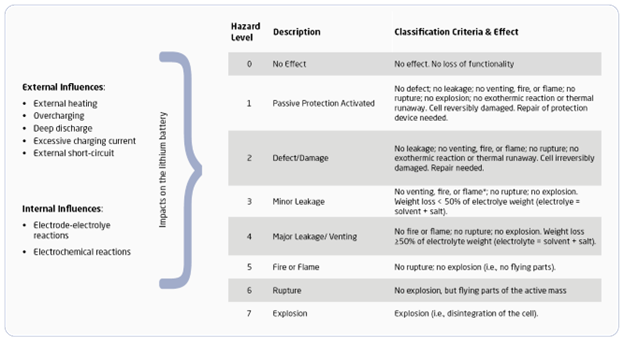
Environmental Test Chambers: Ensuring Safety in testing
Environmental test chambers are an indispensable tool for comprehensive battery testing and research. By simulating the conditions a battery may experience throughout its lifetime, these chambers allow manufacturers to assess battery performance and safety in real-world scenarios before they reach the market. Equipped with the necessary safety features, environmental test chambers are capable of mitigating some of the most serious risks involved in battery testing. Common safety options you may see added to your battery test equipment include the following:
Gas Monitoring
Gas monitoring involves sensors that detect and measure the concentration of potentially hazardous gases emitted during battery testing. This safety feature helps maintain a safe environment by providing early warnings and allowing timely intervention if gas levels exceed safe limits.
Burst Disc
The burst disc acts as a pressure relief mechanism. An intentional weak point, it is designed to rupture at a predetermined pressure, releasing pressure and preventing damage to a window or forcing open a door. This is particularly pivotal during battery testing where pressure variations can occur. The burst disc is housed in a chimney, and the dimensions and quantity are specifically sized for each test chamber as the chimney must be connected to an on-site exhaust system. In the event of a rupture, the burst disc will need to be replaced. To further ensure that violent outgassing is directed through the burst disc, the test chamber liner is reinforced to withstand overpressure beyond the burst disc’s rating.
Explosion Resistant Sheath Heaters
Explosion-Resistant sheath heaters are used to control the temperature within the environmental test chamber. They provide a controlled heating element for the testing environment, and as all electrical connections are made outside of the workspace, they cannot create a spark.
Fresh Air Purge
This safety feature involves a continuous flow of fresh air into the test space to lower the levels of hazardous gases or fumes to keep the workspace below the lower explosion limit. The heating and cooling systems must be sized appropriately because this option could introduce additional air exchanges, and fresh air would need to be conditioned to the test profile being conducted.
Mineral Wool
Extremely resistant to moisture, mineral wool is a special insulation designed for high temperature applications.
Water Spray System
The water spray system includes nozzles so that cooling water can be directed at each battery. This safety feature is increasing in use as it can help prevent a thermal runaway and extinguish fires.
Sprinklers or Deluge System
Sprinklers or a deluge system are fire suppression mechanisms that can be activated in a fire emergency. These systems use additives such as foaming agents or gelling agents that can assist the extinguishing process if an event occurs.
Fire Detection via Gas Monitoring
Integrating fire detection with gas monitoring ensures early identification of potential fire risks. If elevated gas levels indicate a possible fire, this feature triggers an alert or activates fire suppression systems.
As battery technology advances and new applications emerge, so too must testing methodologies and safety standards. By integrating comprehensive safety features into environmental test chambers, manufacturers can stay ahead of the curve and ensure compliance with regulatory requirements. From gas monitoring to fire detection systems, each safety component plays a vital role in protecting personnel and preventing potential hazards.
Understanding these safeties and sufficiently equipping your chamber with the package that aligns with your product’s EUCAR hazard level is an important step in the development process that keeps personnel and product safe. As we navigate the complexities of battery testing, collaboration between manufacturers, and industry partners remains essential. Together, we can pave the way for safer, more efficient battery solutions that power the technologies of tomorrow.
For more expert knowledge on battery testing safeties, check out our white paper on this topic.