Post Curing Ovens for Elastomer Seals
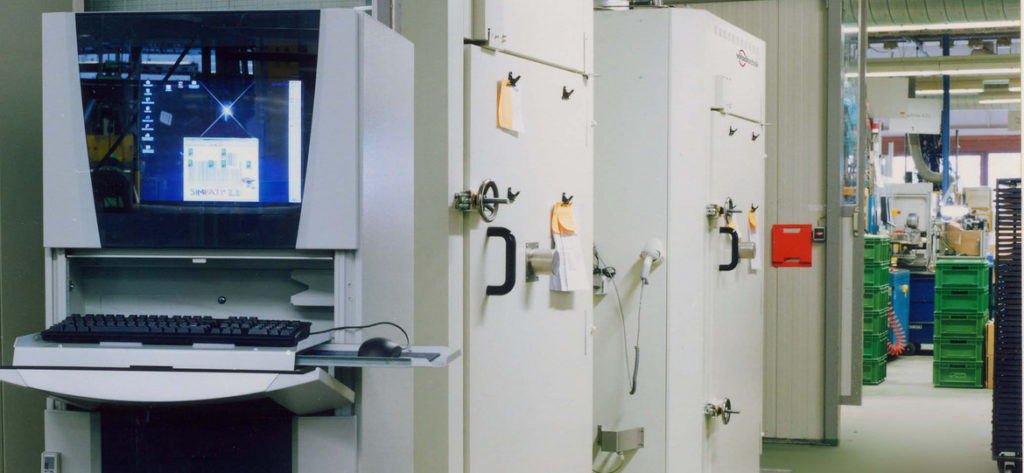
Freudenberg Sealing Technologies, Weinheim (Germany) Safe and efficient post-curing of elastomer seals. Postheating is an important process step in the production of dynamic and static seals made of elastomers. It guarantees the desired functionality of the products and is an indispensable link in the production chain. Freudenberg Sealing Technologies, a leading sealing technology specialist, has been working with individually specified Vötsch standard post-curing ovens for many years across the globe. Currently, more than 100 ovens are in operation – demonstrating the high-quality standard of the company.
Always meeting the highest demands
The post-cross-linking – post-curing or postheating – of elastomer seals after vulcanization is a complex process. Customers, especially in the automotive and industrial sectors, have very high quality requirements. In addition, production must be planned as cost-effectively as possible. To ensure this, all parameters must be optimally attuned with one another, and the process must be safe and reproducible with the technology that is employed.
Holistic process control
Freudenberg Sealing Technologies understands post-curing to be a holistic process with numerous parameters that influence one another. The company focuses on the health of its employees, the safety of its systems, the quality of its products and the sustainability of production (minimization of the carbon footprint).
Achieving reliable post-curing quality
Quality begins with the process. Oven-loading, product geometry, elastomer type, application area and prior shaping cycles all determine the post heating temperature, the characteristics of the recirculating air and the air exchange rate. Once the process has been optimally defined, it must be accurately reproducible to ensure its reliability. This makes it possible to replicate the process conditions at any time and comply with customer- or product-specific procedures.
The technology that is employed has to achieve three things:
- It must be extremely reliable.
- It must prevent operator errors from changing settings and processes. This is realized with smart control systems with permanently programmed processes. Operation relies exclusively on bar codes.
- The design of the post-curing oven must ensure an optimal temperature deviation, even with high loading volumes and air exchange rates. The fresh air volume flow needed for the high air exchange rates is monitored reliably by means of an air volume measurement.
Optimal people and equipment protection
During the post-curing process, by-products and volatile constituents are generated and may adversely affect the health of the employees. In addition, condensate deposits can accumulate in the oven. They increase maintenance requirements and, in the worst case, can cause a failure or even set the oven on fire.
For this reason, it is important to design the post-curing process and the oven in such a way that condensate production is minimized.
To achieve this, the concentration of volatile organic compounds (VOC) must be minimized by increasing the fresh air supply, and by designing the oven so that it does not have any thermal bridges. The oven has a slight internal under pressure and is optimally sealed in order to prevent the escape of even small amounts of VOCs into the installation area.
Ensuring fire protection
The by-products and other volatile compounds produced during the post-curing process are fire hazards and must be removed from the oven as quickly as possible using exhaust air. To make this possible, while considering costs and risks, the absolute minimum amount of air and heat ought to be dissipated. In doing so, it is important to know the emission profile precisely. This knowledge allows the exhaust air to be planned and adapted in an optimal way.
In order to regulate the required volume of supply air, Vötsch post-curing ovens are fitted with a special sensor system. The sensor makes direct measurement possible and is much more reliable than the previously employed technology. It helps save energy and reduces costs and helps protect against fire.
Customized post-curing furnaces
Freudenberg Sealing Technologies has been relying on Vötsch post-curing ovens for many years. They are based on tried-and-tested standard models that have been adapted in close collaboration with the manufacturer to meet the special process requirements at Freudenberg.
Pascal Penoty, Head of Strategic Molding Development at Freudenberg Sealing Technologies, sees the cooperation with Vötsch ovens as essential: “Development is always a dialogue. It is crucial to achieve the defined goals in the best possible way. Thanks to the specific adjustments made to the latest generation of post-curing ovens in order to meet our requirements, we have a significant quality advantage over our competitors.” Any shortcuts involving the key parameters to reduce costs have a direct negative impact on the quality of the final product. “With our Vötsch post-curing ovens, however, we are able to ensure a consistently high product quality and maintain our position as market leaders.”
The furnaces have been optimized, among other things, for airflow and energy efficiency. The process can be fully monitored and documented thanks to Simpati software with a connected bar code scanner. For example, before the start of the process, the oven, the operator and batch must be scanned in before the program is automatically selected and started. This practically rules out any individual errors.
Freudenberg Sealing Technologies – Innovating together
As a leading market and technology specialist in sealing technology, Freudenberg Sealing Technologies is a supplier as well as a development and service partner serving customers in a wide variety of sectors, including the automotive industry, civil aviation, mechanical engineering, shipbuilding, the food and pharmaceuticals industries, and agricultural and construction machinery.