Environmental test chambers are sophisticated equipment that rely heavily on water for humidity generation and system cooling. Understanding and maintaining proper water quality standards for both applications is fundamental to ensuring accurate test results and protecting your investment. Let’s explore why water quality matters and how it impacts different aspects of environmental testing.
Water Quality for Humidity Testing
For humidity testing, water quality plays a pivotal role in maintaining both accuracy and chamber longevity. The process of generating precise humidity levels requires water that meets specific quality standards, particularly in terms of dissolved solids and pH balance. Think of it as similar to a high-end coffee maker – just as mineral-heavy water can clog and damage your coffee machine, impure water can wreak havoc on a humidity chamber.
One of the most visible signs of poor water quality in humidity systems is the formation of deposits and streaks inside the chamber. These deposits aren’t merely aesthetic concerns; they can significantly impact test results and lead to expensive equipment failures. When dissolved solids accumulate on heating elements, they create insulating barriers that reduce heating efficiency and can eventually cause complete heater failure.
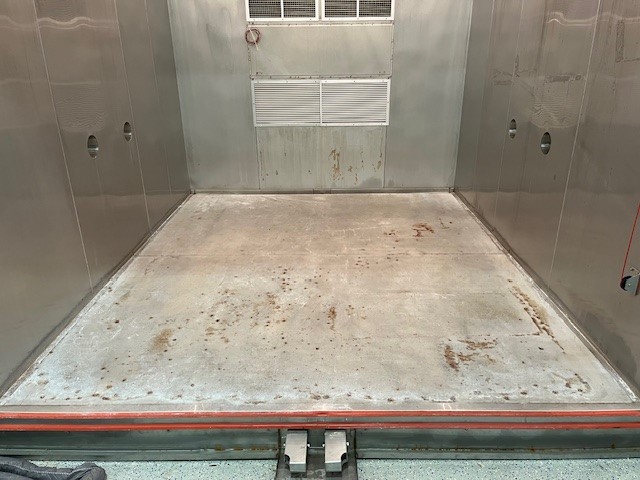
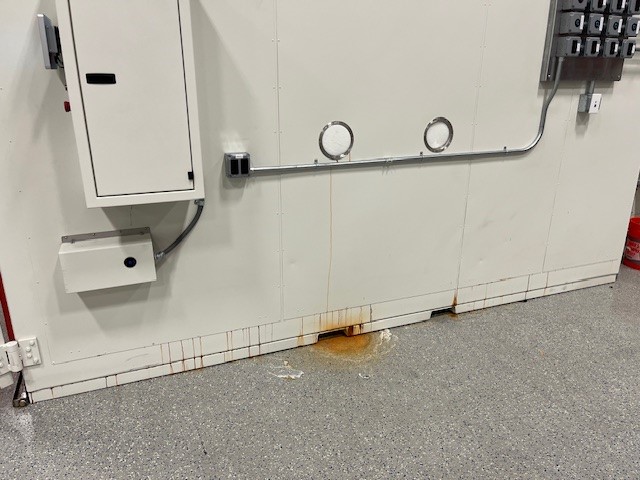
The pH level of water used in humidity systems is equally crucial. Water that’s too acidic or too alkaline can trigger corrosive reactions, potentially damaging both the chamber itself and the products under test. This is particularly concerning when testing sensitive electronics or materials that might react to corrosive environments.
Water Quality for Test Chamber Cooling Systems
The water quality requirements for the test chamber’s cooling system are equally important, albeit for different reasons. Cooling systems in environmental chambers operate much like industrial HVAC systems, where water serves as the primary medium for heat transfer. The quality of this water directly impacts the system’s efficiency and longevity.
Pressure management in cooling systems is particularly crucial. Water pressure that is too high or too low can create performance issues that may lead to system shutdowns. These interruptions not only delay testing but can also compromise test results by creating unstable environmental conditions. Moreover, when cooling water contains corrosive elements, it can gradually degrade system components, leading to mechanical failures and costly repairs.
Water Requirements
While both humidity and cooling systems rely on water, their specific quality requirements differ significantly. Humidity systems demand precise control over water resistivity and turbidity levels to prevent mineral buildup and ensure accurate humidity generation. These parameters must be carefully monitored and maintained to prevent the formation of deposits that could compromise test conditions. Weiss Technik recommends a reverse osmosis or demineralized water supply for humidity water.
Humidity Water Requirements
- Turbidity: Less than 5 NTU* and preferably less than 1 NTU*
- Color: Less than 5 on the pH color scale
- Free Chlorine: Less than 0.2 ppm
- Chloramine: Less than 0.2 ppm
- Chloride: Less than 0.2 ppm
- Total Iron and Manganese: Less than 0.3 ppm
- Organics: Less than 1 ppm (as determined by oxygen consumed)
- Acidity (pH): Between 6 to 7 pH
- Resistivity: Between 50,000 to 1MΩ-cm
Cooling systems, on the other hand, focus more on maintaining appropriate pressure levels and preventing corrosion. The emphasis here is on protecting the mechanical components that facilitate heat transfer and ensuring consistent cooling performance.
Cooling Water Requirements
- Inlet Pressure: 30 to 45 psig (2 to 3 barg), 80 psig max (5.5 barg)
- Pressure Drop: 30 psi (2 bar)
- Grain Size: Less than 1,000 micrometers (20 mesh strainer)
- Acidity (pH): Between 6 to 9
- Saturation Index SI (delta pH value): Between -0.2 to 0.2
- Total hardness: Between 6 to 15 °dH
- Resistivity: Between 0.002 to 0.1 MΩ-cm
- Filtered substances: Less than 30 mg/l
- Chlorides: Less than 100 mg/kg @ 75°C
- Free Chlorine: Less than 0.5 mg/l
- Hydrogen sulfide: Less than 0.05 mg/l
- Ammonia: Less than 2 mg/l
- Sulfates: Less than 100 mg/l
- Hydrogen carbonate: Les than 300 mg/l
- Hydrogen carbonate / Sulfates: Greater than 1 mg/l
- Sulfide: less than 1 mg/l
- Nitrate: Less than 100 mg/l
- Nitrite: Less than .01 mg/l
- Iron: Less than .02 mg/l
- Manganese: Less than 0.1 mg/l
- Free aggressive carbonic acid: Less than 20 mg/l
Water Quality Monitoring and Maintenance
To maintain optimal performance in both systems, regular water quality monitoring and maintenance are essential. This includes:
- Regular testing of water pH levels
- Monitoring dissolved solids content
- Checking pressure levels in cooling systems
- Installing appropriate filtration systems
- Implementing regular maintenance schedules
Investment in proper water treatment and monitoring systems may seem costly initially, but it’s far less expensive than dealing with equipment failures or compromised test results. The quality of water used in environmental testing chambers isn’t just a technical detail – it’s a fundamental requirement for accurate testing and equipment longevity. By understanding and maintaining appropriate water quality standards for both humidity and cooling applications, laboratories can ensure reliable testing processes, extend the life of their environmental test chambers, and avoid the higher costs associated with equipment failures or unreliable test results.
Environmental Test Chamber Water Quality FAQs
Q: How often should I test water quality in my environmental test chamber?
A: Water quality should be tested at least monthly, with pH levels and dissolved solids content checked more frequently if you’re running intensive humidity tests. Implement regular maintenance schedules and keep detailed testing logs to ensure optimal performance.
Q: Can I use untreated tap water in my environmental test chamber?
A: Using untreated tap water can lead to mineral deposits, corrosion, and eventual equipment failure. For humidity systems, this can cause heater damage and inaccurate test results. In cooling systems, it may lead to pressure issues and mechanical failures. Always use properly treated water that meets the specified requirements for each system.
Q: How can I tell if poor water quality is affecting my test chamber?
A: Common signs of water quality issues include visible deposits or streaks inside the chamber, decreased heating efficiency, unstable humidity levels, and irregular pressure readings in cooling systems. If you notice any of these symptoms, immediately test your water quality and consult your chamber’s maintenance manual or manufacturer.